February 8, 2009 archives
you are here [x]: Scarlet Star Studios > the Scarlet Letters > February 8, 2009
<< before
February 5, 2009
after >>
February 10, 2009
February 8, 2009
coraline puppet technology - with photos!
by sven at 4:43 pm
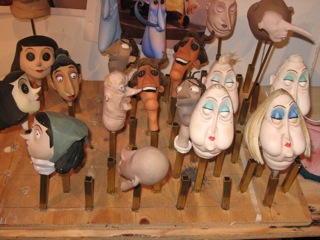
Thursday night I went to the world premiere of Coraline. There's lots to say about the film itself... What has my mind buzzing, though, is the party at the Portland Art Museum that came afterwards.
To convey to party attendees how much effort went into fabricating Coraline's world, Laika/Focus set up stations around the room where people from different parts of the art department had their actual workbenches and stuff they'd created: hair, painting, armatures, knitting, sewing. Amazingly, we were allowed to ask whatever questions we liked and take photos. ...So you better believe I did!
As an indie stopmo filmmaker, I have a powerful interest in puppet construction. So I'm going to share what I was able to learn or deduce. Click on the photos for larger images.
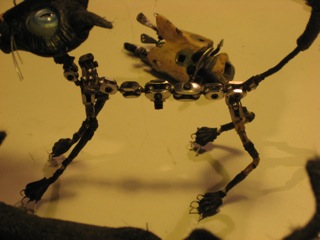
I think that the world of Coraline was produced at 1:8 scale. That means a 6' tall person would be reproduced as a 9" tall puppet. I estimate that Coraline was 7" tall. Stunt puppets at different scales existed for special purposes -- such as the close-up of the sewing needle during the opening credits. I was told that the doll was scaled up more than 2000% for that shot.
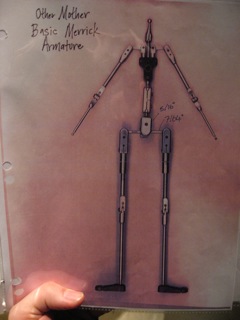
The armatures, were tinier than any I've ever seen. Tie-downs used 4-40 screws -- and that was the largest screw size I saw on any of the armature maps. I recall seeing frequent use of screws labeled 2-56, 1-72 (?) and 0-80. Due to a certain logic inherent in producing step-block joints, it's likely that joints using 4-40 screws also used 1/4" balls. Stainless steel balls are only sold in certain increments: 4/16", 3/16", 2/16", 1/16"... I feel fairly confident that the 0-80 screws were being used in joints that had 1/16" balls and 1/32" rods.
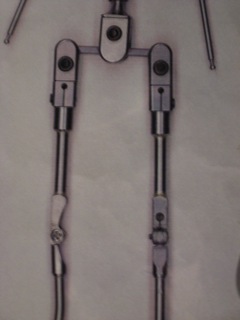
Merrick Cheney down in San Francisco made many of the lead character's armatures. However, it was not uncommon to discover when they arrived in Portland that they would require some retrofitting to fit inside the molds. Most of the armaturists' labor, it sounds like, was a matter of assembling and modifying generic joints. Joints were not being made on premises; the job was outsourced to companies that specialize in small parts manufacturing. Cheney's company produced most of the joints, but there was also another company involved ("Columbia?"). Use of rototools was specifically mentioned with regards to modifying joints for greater range of motion.
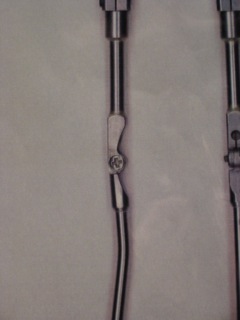
Almost exclusively, the only types of joints I saw being used were step-blocks and double-ball sandwich joints. I did see hinges being used for elbows and knees on some puppets, as well as hinge and swivel assemblies for shoulders occasionally. Sometimes the toe of the foot had a hinge. I saw a surprising variety of ankle configurations, which I'd have liked to study further. I had the sense that some of the chest blocks, with built-in neck and spine balls and hinge/swivel shoulders had been created prior to work beginning on Coraline -- stuff that Cheney had on hand.
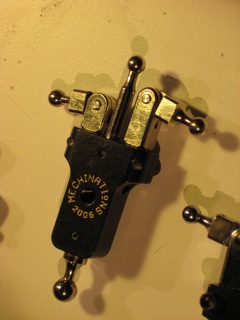
For 1/16" balls, using the usual jeweler's torch would have fried them -- so a butane microtorch was used instead. A special jig was made to hold rod in place, while another tool would hold the ball on top from shooting off. If a ball popped off while brazing, you'd never find it again.
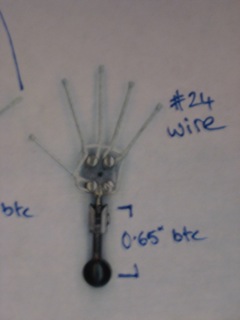
Safety Silv soldering wire was used (not Stay-Brite or jeweler's "hard" silver solder); the person I spoke to didn't recall which grade. For shining armatures, pickle was used. Someone from the rigging department said that after pickling he'd use a brass wire brush, which wouldn't scratch the stainless steel balls. I'm not sure if this was also common practice among the armature makers.
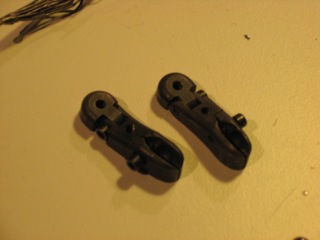
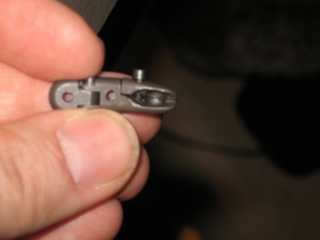
In general, the armature designs I was seeing didn't offer any big surprises. It appears that a standard design has evolved, which is very much like the example that Lionel Ivan Orozco shares in his Armature Anatomy 101 tutorial.
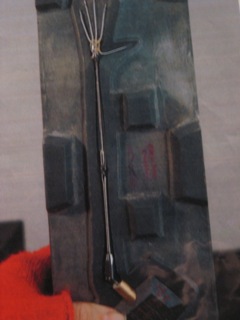
The really fascinating stuff had to do with how the heads were constructed. I saw two basic types of technology.
One strategy involved creating a hollow resin skull with areas carved away where there would be facial movement (mouth and eyebrows, generally). In these hollow areas, there were little metal paddles attached to tiny step-block joints. There might be one or two paddles for each eyebrow, and then maybe three paddles for the upper lip. The actual face was a silicone sheath that would somehow fit over this skull. The Father and Other Father puppets used this technology.
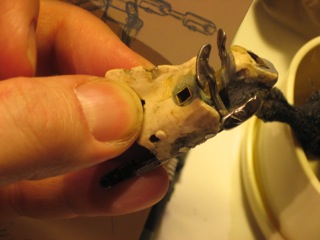
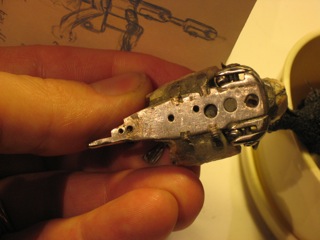
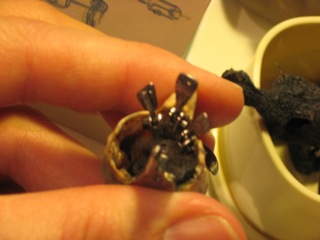
The other strategy was snap-on faces. Faces were divided into two parts: the forehead, and the rest of the face below the corners of the eyes and bridge of the nose. Seams were removed digitally in post-production using Shake (a software similar to AfterEffects). How they managed to do this and maintain the stereoscopic effect, I have no idea.
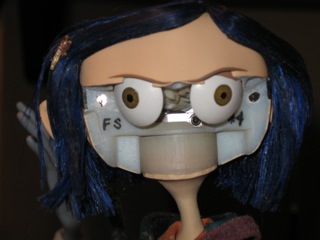
I was boggled at how such precision little parts might have been cast from molds... Until I realized (with some certainty) that these pieces all must have been created using rapid prototyping 3D printer technology. The face shapes, then, were surely created using CG modeling software of some sort. ...Whether or not an original physical sculpt was inputted using a 3D scanner is unknown.
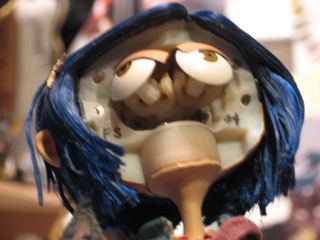
There was astonishingly widespread use of magnets for holding different parts of the puppets together. I'd say the magnets were 1/16" diameter neodynium. Each piece of the face might be attached using several magnets. I wondered if the orientation of the magnets mattered, since magnets can repel as well as attract -- but didn't think to ask. Puppets like Coraline and Wybie used the hair and chin lines to their advantage; Bobinski and the cat were different, making use of smile lines to hide seams.
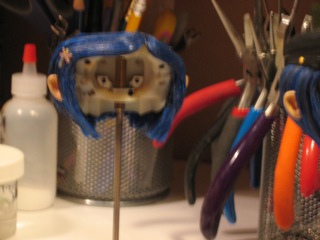
Coraline's eyes were flattened hemispheres that were attached to the skull behind the two-part snap-on face. I was very surprised to see that they were attached using resin joints rather than metal ones. I'm still having trouble figuring out what I saw, but it seemed that the ball-capture plates were attached to the back of the eye, and a ball was attached to the skull. I think the eyes may have actually used plastic universal joints -- but as I said, I'm still confused. Eyelids could rise and lower and had their own separate joint mechanisms in the skull, squashed in with those for the eyes.
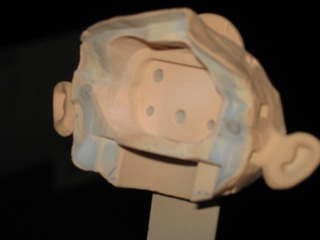
Some characters appeared to have K&S plug-ins for eyes. I didn't see any collections of eyes with square-shaped plugs on their backs, so I'm somewhat confused by this. Eyes in general didn't have holes in the retina (as is common for puppets)... So when the animators used sharp things to move them, the eyes were frequently damaged, irritating the folks in charge of fabrication and repair.
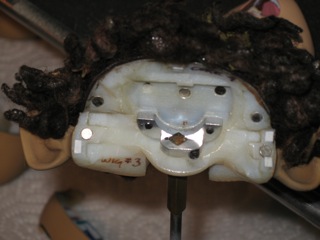
The heads generally had squat cylinder-shaped cavities at the base where the neck connection could be concealed. The neck-to-skull connection generally involved square telescoping K&S... But rather than being cast or glued into the skull, I saw steel bits at the base of the skull that allowed you to capture the K&S with a screw.
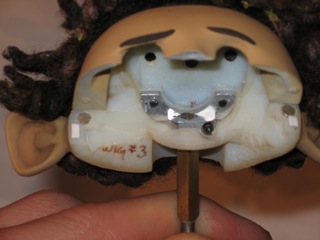
With the exception of the Other Mother (a special case), I didn't see any jointed hands. Hands were made from thread-wrapped floral wire. I saw one hand design that had a wrist ball attached to a flat palm, which had four screws for capturing the wire fingers, all made from one piece of wire. A threaded tie-down hole was also placed in the palm.
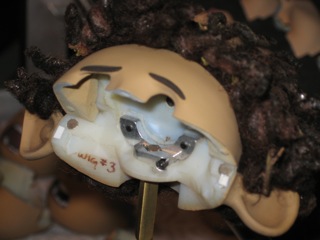
It was impressed upon on me that rigging points in general should never be round -- they should always use telescoping square K&S to prevent the puppet from accidentally rotating around -- as might happen, were you to only use a threaded rod.
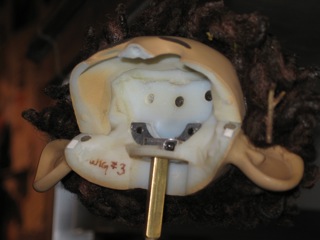
Wigs were made from synthetic hair and sometimes mohair. Natural fibers were too subject to expanding and contracting with changes in temperature. All the fibers were hand-dyed. They'd be held together using massive amounts of a hair-styling fluid with the consistency of water, painted on with a brush. It sounded like the wires in the hair were usually thread-wrapped floral wire. Lay down the wire, then lay down the hair on top of it. Pony tails and other large hair sometimes had ball joints hidden inside, for the sake of being animatable. Thus, the hair department sometimes had to collaborate with the armature department.
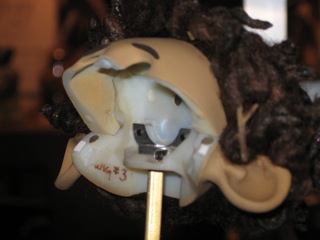
For certain puppets, aluminum wire was cast inside the silicone skin. This was the case with the scotty dogs and with the melting Other Father's mouth. With the Other Father, The wires didn't form an "O" as one might expect -- they were perpendicular to that.
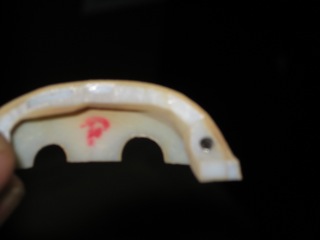
Both silicone and foam latex were used for puppets. (A bit of a surprise: I recall reading an interview back when "Life Aquatic" came out saying that Selick was never going to use foam again.) Coraline's dad had a silicone head. Forcible and Spink had foam latex bodies... Presumably because such bulky puppets would have been too heavy otherwise.
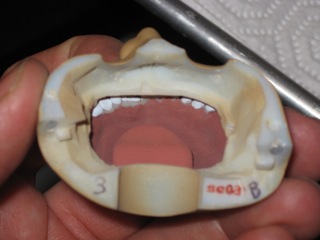
The folks on this project worked 50 hour weeks during the entire course of the production. One person I spoke to said that this might not be the case if Laika does future feature films. This person thought Laika had learned its lesson: You can work at that pace for a month or two -- but after two years, people were simply too exhausted. It cut down on productivity to the point where 40-hour work weeks may have been just as effective.
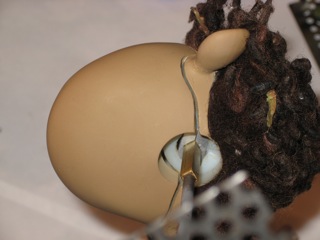