you are here [x]: Scarlet Star Studios > the Scarlet Letters > mass producing joints
<< before
mhcc calligraphy: class 10 (final project)
after >>
process and product
March 25, 2006
mass producing joints
by sven at 11:59 pm
A week ago I showed off my first successful brass "open hole double ball" joint. Since then I've been working on figuring out how to mass produce these things.
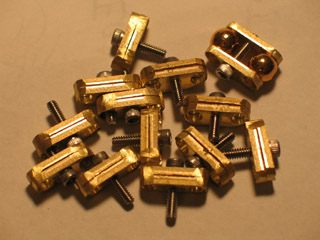
The photo above shows where I got to tonight. This is my second attempt... And I expect there'll be a third. When the process is perfected, I want to do a tutorial.
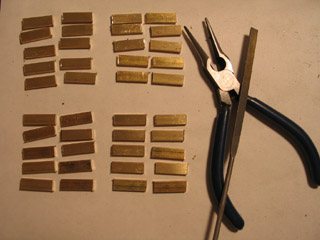
With my first attempt, I started by cutting forty 18mm-wide plates. That was a mistake.
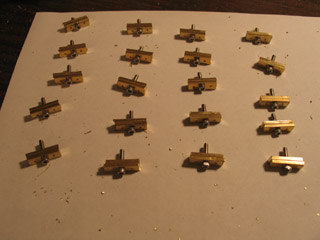
Problems with attempt #1: It was incredibly fiddly getting the parts in and out of the vise... The plates weren't always perfectly even with one another...
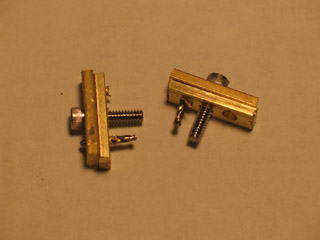
...And I broke two drill bits -- I believe because the drill would knock against the head of that screw as it punched through the brass strips.
Drat. I had a batch of 20 joints getting close to completion. But then I discovered the design (or rather, the process) was fatally flawed.
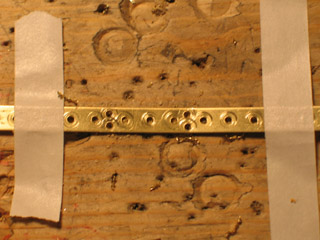
I was in the middle of a conversation with Gretchin, and suddenly stared off into space... Ah-ha! A new idea for how to mass produce these joints!
The gist: Rather than do one joint at a time, bind two strips of brass together, drill all the holes, and then cut the strips into pieces.
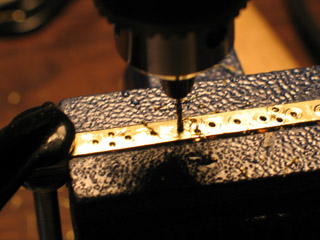
This time I made a template out of a thin piece of metal. It turns out that the template strip was too thin (it curled!) -- and I also drilled more holes than I actually need -- but the concept is sound.
When I got around to using the template to drill holes in the plates, I used lubricant for the first time. Just water -- but the difference was noticable nonetheless.
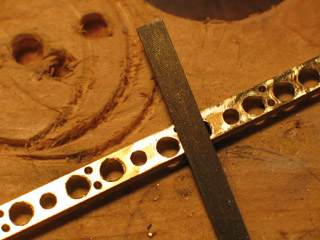
The K&S brand brass strips I'm using are .093" thick, 1/4" wide, 12" long. K&S has seven standardized displays that they send out to retail stores. The .093" thick stuff is only sold in their "jumbo" hobby metal display. I can name six stores in Portland that sell K&S -- but only one has the jumbo display.
I bought the last two strips in the store last Sunday. I used these up in the failed first attempt Monday. ...Waiting until Friday for the store to get new stock in was murder.
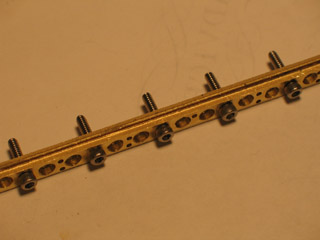
On the first attempt I used a fine-point Sharpie to mark measurements, and a hammer and a brass screw to start holes. For my second attempt, I used a metal scribe and a center-punch to make the template. It's my first time with these tools, and they helped a lot.
In the picture above you see the two strips fully drilled, and I've added 1/2" 4-40 stainless steel socket cap screws. Adding them in after all the holes have been drilled, I didn't have the same problem with breaking bits this time.
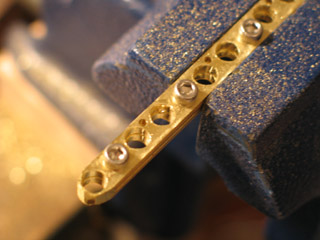
For cutting the individual joints off of the strip, I used a Dremel with a reinforced cut-off wheel. I tested normal cut-off wheels, and a jeweler's saw first... The jeweler's saw gave a nice hair-line cut -- but I broke two blades on my first two cuts -- so I'll be reserving that tool for finer work. The regular cut-off wheel made a cut 1/32" wide, whereas the reinforced wheel made a cut 1/16" wide. Given the amount of cutting I'm doing, durability won out.
Even with it being reinforced, I've worn one blade down from the size of a quarter (larger, actually) to the size of a dime -- and another splintered and flew at my face. Thank goodness Safety Boy is fastidious about wearing his safety goggles!!
An unforseen benefit of cutting the joints off of a strip: immediately after making the cut, I can round off the joint on one side. ...You see, this is such a time-consuming process -- every motion that you can eliminate from the workflow makes a difference.
I think I'm going to need 17 joints to make an armature. If they all prove functional, it looks like I got 13 done tonight. I may just try to salvage the remaining four from attempt #1.
--But there will be an attempt #3 -- and soon. The process is so close to being right...
posted by sven | March 25, 2006 11:59 PM | categories: stopmo